|
Body and neck both need a little final carving and shaping then a good spell of sanding to get all the surfaces nice and smooth. Will update as it moves along.
|
Left: Getting back to this bass after a long busy spell - I need to get the neck attached to do some final shaping and carving. Also need to decide on a color tint!! Right: I'm now plannng on creating a nice radius around the body front and back and locating the bridge in place. Might also cut an arm relief curve at the top of body. |
Getting ready to establish a nice radiused edge break around the front and back of the body. Also going to set retaining screw holes for the bridge.
|
|
Pickup covers machined and now I have to cut two recesses based on the bridge location to house the pickups.
|
Left: I have machined the two pickup covers and I am now hetting the body of the instrument set up on the CNC so that I can machine out the two pickup recesses. Right: I have machined the two recesses for the pickups which helps move this instrument along! I'm going to be sanding and shaping to get it ready for finishing. |
I was able to machine the two pickup recesses into the top of the body!.
|
|
Will be using an Audere 4-band preamp which uses three stacked control knobs.
|
Left: Been doing some machining on the body. The recess for the Neutrik jack socket has been established and I machined the holes and counterbores for the control knobs. Right: I have the completed pickup bobbins for this bass but will probably manufacture the pickup covers. I'm designing them on computer right now. |
This is close to the cover design that I will end up. Have to machine them on the CNC first!.
|
|
This bass is not very far from finishing so I want to get a final shape and thickness on the neck and cut a nut slot so that I can install a nut.
|
Left: I removed the neck so that I could machine a nut slot at the headstock end and also to work on the neck thickness and profile so I could get them to a finished stage. Right: This is a back view of the instrument right now. All the center body laminates and those of the neck are tapered and match so the back will look awesome! |
Not sure yet whether the back will have a clear coat or a tint but either way it will look impressive.
|
|
I attached the neck so that I could get bridge and pickup locations established. It also allows me to do some final neck shaping to get it ready for finishing.
|
Left: I drilled through the body in the neck pocket so that I could bolt the neck onto the body of the bass. This allows me to accurately place bridge and pickup locations. Right: Time to establish the two pickup positions and sizes and the location of the bridge so that I can get some of the final machining operations done. |
I attached the neck so that I could get bridge and pickup locations established. It also allows me to do some final neck shaping to get it ready for finishing.
|
|
These are a set of J-Bass pickups I had would some time ago. Just re-tested them to make sure they were still ready to go.
|
Left: I have two J-Bass pickups wound and ready for use in this bass. I'll be cutting the pickup recesses for these and hopefully will have the whole instrument ready for finishing very soon. Right: I will be putting a German Schaller bridge on this bass. Once I have the neck bolted on I will plot out the locations for the bridge and pickups. |
This will be an unusual J-Bass anyway and I like the Schaller bridge and how it is constructed. Should work out fine.
|
|
Getting ready to mchine recessed holes for the neck attachment.
|
Left: I now have the body of the bass up on the CNC so that I can accurately place and machine the four recessed holes that will allow the neck to be bolted on to the body. Right: The holes and recesses for the neck attachment and support rings have been drilled through and now ready for me to attach the neck to the body. |
I can now attach neck and body and that will then allow me to plan out the placement for the bridge and pickups.
|
|
Machining the control cavity from the back of the body.
|
Left: Decided to not use a metal J bass plate on front, I'm going to machine a standard control cavity in the back and leave the front clean to show off the grain and finish. Right: The control cavity is now established in the back of the body. I will make a lid for this from the same mahogany material. More body and neck shaping to come soon. |
The control cavity is now part of the body. Next will be some shaping and contouring of body and neck.
|
|
Sanded out the belly cut - will have to cut some cavities soon for pickups and electronics.
|
Left: Got the belly cut leveled and sanded to a finished condition. I will create edge break radii around the perimeter of the front and back of the instrument body. Right: Due to other emergencies I haven't been able to get a lot done on this J-Bass recently. Probably going to use standard Jazz style pickups to maintain the J-Bass theme. |
Standard Jazz Bass pickups should work fine n this bass. Combined with the 4-band Audere EQ it will have plenty of sound.
|
|
Tuner holes now drilled through headstock.
|
Left: Holes for the tuners have now been drilled through the headstock. I'll do a little cleanup around the edges and this part will be done. Right: I was able to get some roughing work done to the belly cut area on the back of the body. This creates a more comfotable instrument and also mitigates some body weight at the same time! |
Belly cut roughed out. Will now file and sand it till its perfect.
|
|
Testing a Hipshot bridge to make sure it would work for this project.
|
Left: I will be using a hipshot chrome bridge on this bass so I'm now checking placement and string spacing to make sure this bridge will work. Should look great against the finish. Right: Got the truss rod slot back into the headstock after the veneer was applied. Now I'm going to drill the five holes for the chrome Hipshot tuners. |
Headstock ready for tuner holes.
|
|
I know my finisher can do a spectacular job in creating a finish that will match this beautiful shell inlay.
|
Left: The top of this bass is an awesome curly/quilted maple which will look amazing after finishing. I'm considering applying a finish to match the various colors in the neck inlay! Right: Currently working on applying a curly maple veneer over the headstock so that when the instrument is colored and finished it will all match!! |
The veneer on the headstock will permit matchig the body finsh on the headstock too.
|
|
I will be cutting the neck pocket soon but before that I wanted to decide which bridge to use.
|
Left: This photo shows the neck and body together although I haven't cut the neck pocket yet. Thinking of using this Schaller bridge if the string spacing is right. Right: Neck pocket has been cut and the neck fits in the body nicely. I will be doing some trimming to the body now to finish up the outer profile. |
Neck pocket complete.
|
|
Frets about to be installed and when they are done I'll clean up the ends and remove the board from the MDF substrate.
|
Left: Now bending the fretwire and cutting it to length so that they are ready to install. Once they are in and cleaned up the board can go on the neck. Right: Fingerboard finished and now being glued onto the neck blank. Once this is set I can clean it up and shape the neck and also work on getting it attached to the body! |
Attaching fingerboard to the neck.
|
|
I only do two inlays at a time because it makes everything a lot more manageable.
|
Left: I was able to get all the shell inlay installed in the fingerboard today so I feel that this bass moved forward a little bit! I'm going to seal the inlay and clean up the surface next.. Right: This is the fingerboard with the surfaces sealed and leveled. Before frets go in I will also apply a sealer to the wood which will make it darker. |
Inlay has been sealed and leveled.
|
|
This bass will have a really cool looking shell block inlay on the fingerboard.
|
Left: I'm currently working in getting the shell inlay installed into the fingerboard. This is an example of the shell that I will be using - should look great against the finished color of the wood. Right: I am carefully cutting out the shell inlay and progressively installing it in to the recesses I caut in the top of the fingerboard. |
I only do two inlays at a time because it makes everything a lot more manageable.
|
|
Machining on fingerboard complete - it's now ready for some inlay pieces.
|
Left: Fingerboard has been machined to size - compound radius has been machined on the top surface and fret slots cut into the top. I also cut the recesses for the block inlay. Right: I have cut inlay support pieces in the laser and fitted them into the recesses and then sanded flush with the compound radius. |
Adding substrate pieces that will eventually be attached to the inlay shell.
|
|
Body is getting close to being ready for machining.
|
Left: I'm sanding around the perimeter of the body to the point where I can call it complete as far as overall shape is concerned. Need to get back to the neck now. Right: I chose a fingerboard material and have it on the CNC right now cutting the perimeter to size. Next will be the compound radius and the frets slots/inlay. |
Fingerboard under construction - trying to get this bass into a more complete condition.
|
|
Gluing the carbon fiber rods into the neck assembly.
|
Left: Clamping the two carbon fiber reinforcing rods while they are being glued into the neck. Once this is done I can plan on getting fingerboard attached. Right: Two carbon fiber rods are glued in and I have carefully leveled the surface flat again so that we are now ready for the addition of a nice fingerboard! |
Thet 2 CF rods make a huge contribution to the rigidity of the neck.
|
|
Body and neck are going to get some more attention in the next day or two.
|
Left: Neck and body will be getting some more sanding work - I'm also getting ready to install the two carbon fiber support rods into the slots I cut in the neck. Right: Carbon fiber rods cut and fitted to slots - I just have to get the glue mixed and I can get these installed into the neck. The add strength and rigidity to the neck assembly. |
Thet 2 CF rods make a huge contribution to the rigidity of the neck.
|
|
Marked out location of neck recess - first chance on cnc I will get that cut!.
|
Left: Not much time to work on this bass due to the priorities of the custom work I am doing. I did get the body and neck markes for cutting the neck recess into the body. Right: I decided to use a Rosewood fingerboard as it will blend nicely with whatever treatment we give the final instrument. |
Rosewood fingerboard attached to substrate for machining.
|
|
Neck with the heel end machined down to final thickness. The tapered lamnates match exactly!.
|
Left:This photo to shows the match between the neck laminates and the body core laminates which end up creating a continuous tapered theme through the whole bass. Right: Time to get things moving on this bass again so that I can get it up for sale! I cut and rough shaped the headstock today. |
Headstock now much closer to finished profile.
|
|
The neck perimeter has now been established.
|
Left: I have now machined the perimeter of the neck to its final size. Next task will be to cut truss rod and carbon fiber slots. Right: More machining completed and now we have the truss rod slot cut and the truss rod sucessfully fitted into the neck. All I have to do now is cut the two slots for carbon fiber rods! |
Got the truss rod slot geometry machined into the neck!.
|
|
Starting work on the neck.
|
Left: The neck of the bass is up on my CNC and I have just surfaced the top joint face. I will also be cutting it to its final widths and machining the headstock area too. Right: I machined the upper surface of the headstock with its curve up to the neck surface. I will veneer this surface to match the body top. |
Cutting the headstock surface.
|
|
gluing the top plate onto the body in the vacuum press.
|
I have had this bass on the shelf for a long time and haven't done anything to it because I have been simply too busy to get to it. I saw it today and thought I should try to get it finished since it could end up being someone's favorite 5-string bass! It has all the ingredients for being a really awesome J-Bass and the top will look great with a tint. As time permits I will get the neck machined so that I can fit it to the body! |
|
gluing the top plate onto the body in the vacuum press.
|
The body and top are now being glued together inside the vacuum press. This method allows even pressure to be distributed over the entire surface of the body and ensured a very clean and even joint. Getting the top glued on allows me to be able to cut neck pocket, pickup holes, control cavity and a number of other features. It shoul dend up being a beautiful looking bass as the top wood is quite impressive! |
|
Top plate prepped and sanded - ready for assembly.
|
This is the maple top plate which I am preparing so that I can get it glued onto the instrument body. It has been sanded both sides and has had some decorative veneer applied to the underside joint face. This maple top will look very nice when finished and will give us many options on color tints if we decide to go with a color or a sunburst. There is a lot of really nice figure in the grain of this top so we will do something cool to bring it out! |
|
Body being machined on CNC.
|
I have the body blank on the CNC just to clean up the top surface. It will be drum sanded so that it is ready for the top plate. The combimation of the maple and mahogany always works well for a bass like this both in sound and in aesthetics. The multi-laminate neck will be very strong and the neck and body core will look really nice together. Now I have to get the parts glued together so that I have a complete body to work with. |
|
Quilted maple top ready to glue together for the top plate.
|
This is a photo of the two top plates after having been machined so that they can be glued together. I know that this curly maple material will look awesome on the finished instrument and also that it will accept any color tint that may be necessary. If I don't get a buyer by the time I have to finish this instrument I will probably use a transparent black or a sienna sunburst. Either way it will look very impressive! |
|
Top bout of the body being glued onto the core.
|
I cut the top and bottom body bouts out of mahogany and rough sawed them to shape. I then machined accurate joint faces on each piece. I maple veneer was glued onto each joint face and the sub-assembly was then cleaned up. Now I am able to glue the body pieces together. In the photo the top bout is being glued onto the body core. I'll add the bottom bout as soon as I have time and we'll have something that looks like a bass! |
|
Core of the body and the neck laminates are now glued together.
|
All the various tapered components have now been successfully glued together. I can now start the machining process on each of these pieces. I want to get the rest of the body cut, machined and assembled so that I can glue the quilted maple top on and have a complete body to work with. The neck will go up on the CNC soon for various machining operations. They are looking good so far - very lightweight and resonant. |
|
Gluing the tapered laminates of the nack and body.
|
I am busy gluing all the tapered laminates together. Each one of them has had a contrasting veneer glued to both joint surfaces, and when they are all together that will create a very attractive double pinstripe between each tapered laminate. A lot of detail work involved in that - but I always feel it is well justified in the finished product. I want to get this bass to the point where it is a complete assembly as soon as possible. |
|
Top plates veneered and ready to glue together.
|
I am using a nice piece of quilted maple for the top of this bass. I have already resawn it from its parent material and sanded the bookmatched pieces to the finished thickness. I then glued two veneers to the bottom surface as a decorative highlight. They are now reay to have the joint faces machined. That will allow me to glue them together into one complete top. It is still a littl;e oversize until I glue it onto the body. |
|
The tapered laminates are ready to glue together.
|
The separate tapered laminates have been machined and vaneered with dark veneer against the light woods and light (maple) veneer against the dark woods. They are all now ready to be gued together. Once these laminates are glued together we will have a neck blank and a body core that will allow us to move rapidly forward. The materials we are using will yield a great tonal response so I am looking forward to seeing what this bass will dweliver!!!! |
|
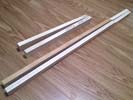 |
From humble beginnings... I just got this bass started. A few days ago I made a couple of new templates that were updated based on my last batch of J-Basses (which came out very well). These upcoming ones will have a few engineering changes to keep raising the bar towards the best a J-Bass can possibly be. This particular one will have a maple and sapele neck. In the photo I have rough sawn the forst few pieces of maple. |